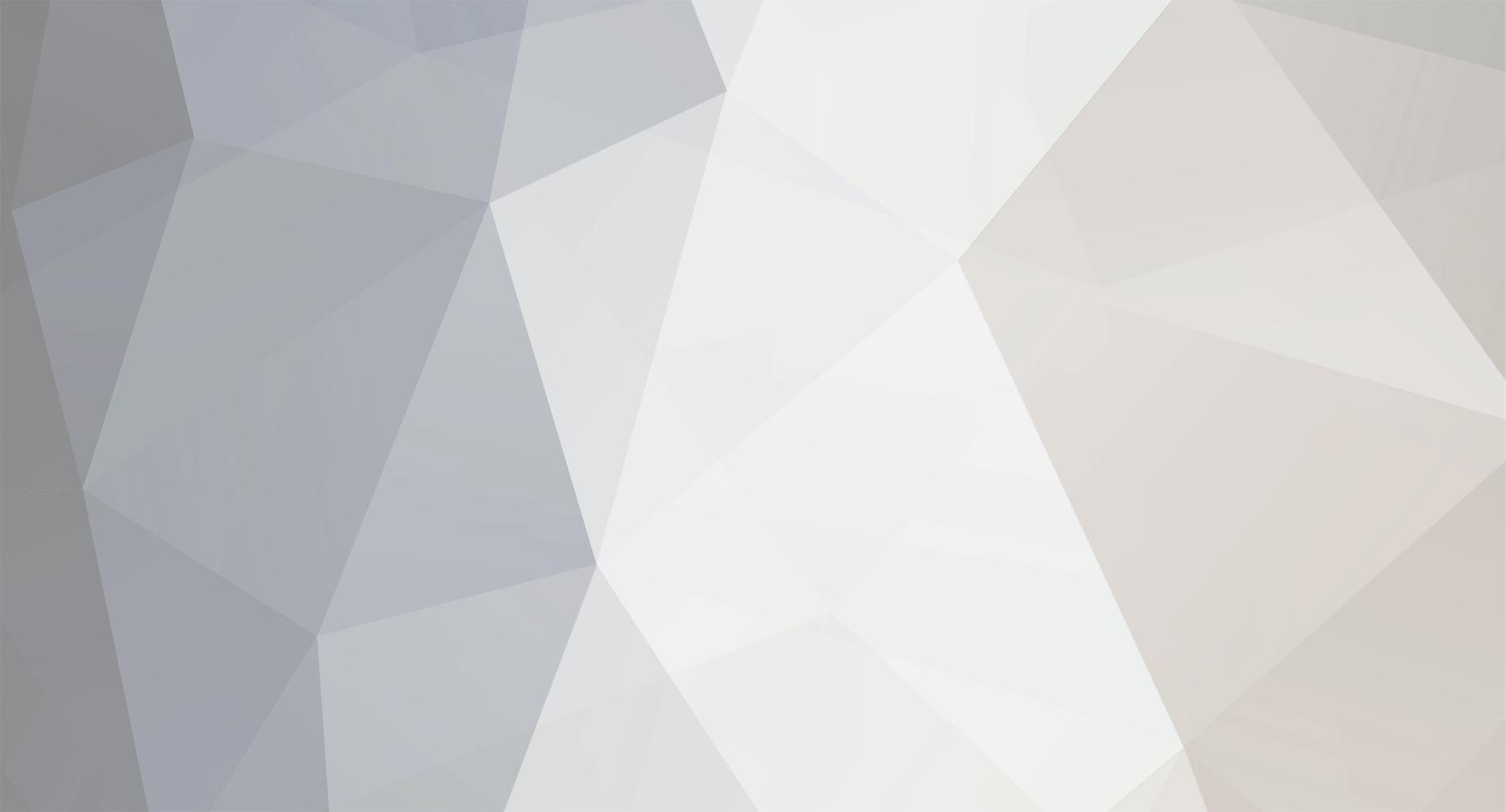
Sewdhull
Members-
Posts
591 -
Joined
-
Last visited
-
Feedback
0%
Content Type
Profiles
Forums
Buy a Patch
Classifieds
Everything posted by Sewdhull
-
Need a spade connector.... what size, and where from?
Sewdhull replied to RostokMcSpoons's topic in Electric Guns
I'm tired, probably lacking in sense of humour. To no one in particular, crimping properly creates a molecular bond between the metals impervious to moisture, where soldering sticks the wires and connector together. -
Need a spade connector.... what size, and where from?
Sewdhull replied to RostokMcSpoons's topic in Electric Guns
I dunno, those connectors are supposed to end up with the tabs bent back in a u shape. A good crimp is better than a soldered joint, but a poor crimp will loosen and the cable not make proper contact, get warm and fall out. 2.8mm connectors are a bit small for these motors, some automotive connectors are better but the fit might be an issue. If you don't have a decent crimper you're better off soldering the wire to a pre-bent connector, crimping the insulation for cable relief then heat shrinking the lot. -
Need a spade connector.... what size, and where from?
Sewdhull replied to RostokMcSpoons's topic in Electric Guns
A good crimper matters. Poor crimping will let go and can result in bad things happening. If you choose to solder them bend to shape before hand and only solder the inner crimp, but I would choose crimping over soldering. This place is good. I've ordered stuff from these guys before. -
I suppose it's worth saying that bushings would end up wearing the same place making lubrication tricky and that bearings would see a load biased to one place but because the balls spread the load over an area it outer race would wear in a similar place to a bushing but the lubrication would still spread.
-
I think that's right altho i am just starting my 5th night shift. Remember these are not forces of the gears pushing against each other, they dont as they at times not in contact with each other. The forces are created when the gear teeth mesh at an angle and push at an angle creating forces in 2 or 3 directions. The down arrow for the Middle gear i wrong, it should be up.
-
The forces get resolved for each gear and they originate at the motor. Forces balance, the tangential forces that spin the gears only do so because there's more motor force than needed to compress the spring. The axial and radial forces balance at each bearing. The forces originate at the motor pinion and build depending on the load the gears eventually connect to. The gear teeth meet at an angle which produces the radial and axial forces dependant on the gear types and gear shape.
-
what forces do you want on there, parts are missing...is it the forces on each bearing you are after?
-
Need a spade connector.... what size, and where from?
Sewdhull replied to RostokMcSpoons's topic in Electric Guns
The heschen female connectors 2.8mm from amazon are good quality compared to some of the rubbish out there. They feel right too. 3.79 for a bag of 100. -
For a bevel gear the axial force is around double the radial force, which I took as 1N so axial force is 2. The calculations are done on the linked gear page. The 3N is derived from the interaction of the Middle gear and Bevel gear 3 to 1 ratio multiplying the tangential forces and proportionately increasing the radial force. It should be noted that gear tooth geometry affects the forces, the pressure angle in particular, but a little research indicates that the numbers on the linked page are typical.
-
If it's snug you can prevent the bucking deforming as it's assembled with a little silicone grease. For Airsoft guns, lithium grease for metal and silicone for rubber and plastic. The loads and temperatures are moderate so a moly grease for example is unnecessary and stickyness is probably more important than lubricity etc.
-
I wonder if bearing and bushing placement exists because that's what people say it should be like and that's what the customer then expects, or perhaps because you can do a crap job with bushings and the gun will be ok. A V2 or V3 gearbox has very similar gear alignment, it could be identical... I haven't checked. TLDR; Radial force is a force at 90 degrees to the gear shaft, an axial force is in line with the gear shaft. The radial force on the bevel of the Bevel gear ( proportional to the tangential Force turning the gears) is a made up 1N of force to provide some illustration of the relative forces in an 18:1 gearbox, this is not torque nor what the forces actually are. Only the bevel end of the Bevel gear bearings experience axial force, the bearings at the bevel end get an upwards radial force (1N) the other end a downwards radial force (3N). The axial force would be 2N on the bevel end. The Middle gear has its radial forces all at one end of the gear shaft resulting in only about 25% of the force going into the bearings furthest from the gears and the force pushing up and back into the bearings at about 9.3N a the gear end and 3.1N at the other. The Sector gear has the radial forces applied in the middle of the gear and tending to push forward into the bearing and down. It experiences the highest forces, but these are shared evenly between the 2 bearings, with about 11N each. If you are worried bearings wont cut it, bush the Sector and the Middle bearing near the gears. If you aren't, then bearings everywhere. I've looked up the Newton ratings for some airsoft springs, an M120 spring was 80Newtons and someone else did some calculations for spur gears, it looks like 100N of tangential force causes 36N of radial force for those gear teeth on the web page. Looking up bearing specs it seems even the static load at 140N, rising to 460N dynamic will be fine for an 80N spring producing 28N of radial load spread between 2 bearings gives 14N for each bearing, 10% of static load and 3% of dynamic load. Lubrication and shimming matter too, you need small <6mm shims for bearings otherwise you shim to the outer race, bypassing the spinny bit. No need to lube shims with bearings, nor gear shafts, just the bearing, regularly. Anyway, thats probably enough of that. Taking the Bevel gear, forces are created by the meshing of the pinion and bevel and leads to an axial force away from the pinion through the bevel onto the bearing or bushing via the shims and a radial force onto the bearing or bushing via the gear shaft again away from the pinion, the gear turns by the tangential force. This gear sees the lowest forces, axial force excepted. The Bevel gear shaft then turns the middle gear, from its sector gear section creating no axial force, a radial force and a tangential force acting on the Middle gear. -The Bevel gear experiences radial forces in almost opposite directions at opposite ends of the gear, up at the bevel end and down at the sector end, and an axial force towards the bevel end of the gear. The Middle gear has a radial force opposite to that on the spur gear part of the Bevel gear, the tangential force from the Bevel gear turning the Middle gear which creates a radial force from its interaction with the Sector gear spur and a tangential force which turns the Sector gear. -The Middle gear experiences radial forces at about 90degrees to one another, almost at the same place on the gear shaft, up from the Bevel gear spur and back from the Sector gear spur. There are no axial forces. The Sector gear has an opposite radial force from the Middle gear spur and a radial force from the interaction of the outer spur and the gear rack of the cylinder. -The Sector gear experiences radial forces forwards and down, close to the centre of the Sector gear. -The cylinder rack experiences a rearward and upwards force from the Sector gear. https://khkgears.net/new/gear_knowledge/gear_technical_reference/gear_forces.html#:~:text=In the meshing of a,force acting on driven gear. https://www.smbbearings.com/firebrick/ckeditor/plugins/upload/Uploads/Documents/bearingpdfs/SF693-stainless-steel-flanged-miniature-bearing-3x8x3mm.pdf http://airsofttech.dk/Guides.cshtml?Page=SpringRating
-
Oh pins...I should look better too, or not post on night shift
-
Who would want a loose screw anyway...
-
I'm choosing to stay ignorant of my spending, nothing good can come of that knowledge
-
I should read these things properly. There's a squarish seal in the bottom of magazines you can get to if you unscrew the bolt in the bottom. A metal block can be removed then to expose the seal. Lube that, make sure it seats correctly or get a new one. You can safely ignore the rest of this reply. You can try a drop or two of silicone oil in the hole and blip a little gas in. I suggest purging out the oil after this with gas. Or remove the valve and do the same ( my preference) Or finally get new valves.
-
Batteries shouldn't make any noise and after 6 years of no use might well be useless now. In any case I'd be getting a new battery which may be all the problem is. Take the motor out and connect the power back to it and see if it runs. Try to stall the motor by hand, use a rag to hold pinion otherwise if is does have some torque you'll lose some skin.
-
A Call for Revolution: Supercapacitors in Airsoft
Sewdhull replied to Pseudotectonic's topic in General Discussion
I think if you have a supplementary power source, esp something like capacitors, you will take some of the load off the primary power source. Those smaller caps are likely to have much lower esr than the larger ones and may be able to supply a burst to help the battery whose voltage is sagging which is significant. Getting enough energy out of them to matter would be the issue. There are some some fairly standard caps of 47000uF 16v with 13mOhm ESR. Sadly they would only give you 47mA for a msec for each volt they were above battery voltage, but could supply 77A. getting the right cap for the job, esp given what is available its tricky and you may have found the best cap already for the task. -
I think all the brands, gate, aster, leviathan and perun do v3s which do away with the trigger block. The perun is the cheapest at around 60 quid. I've realised your moving the trigger out of the gearbox so none of those would work for you. Perhaps more details about what you are mounting your trigger in? If it's from scratch you could hack up an old gearbox section and a normal trigger and block with a bog standard MOSFET.
-
It's a good point, red dots will typically be used both eyes open, is something to learn I guess if you don't normally.
-
Depends what you want to spend, how they look etc but both dots are smaller than a man's head at 100m, in excess of Airsoft gun range. Dot quality does matter, they can get glary from optic reflections.
-
A Call for Revolution: Supercapacitors in Airsoft
Sewdhull replied to Pseudotectonic's topic in General Discussion
You can measure or calculate IR using voltsdrop as you have, apply an oscillating signal using a meter to measure it or a small and larger current to get a better idea of the IR. I'm curious as to what could raise the inrush current then drop it as spring rates rise, then raise it again as the spring rate rises again.. My thoughts are that it's a limitation of instrumentation, but I don't know why that would be. This happens for the non specna motors.. The other currents rise with increased loads on all the motors. https://www.benzoenergy.com/blog/post/battery-internal-resistance-and-its-measuring-method.html/ There's a description the AC measurements there. -
A Call for Revolution: Supercapacitors in Airsoft
Sewdhull replied to Pseudotectonic's topic in General Discussion
Inrush current or peak current, not to be confused with current under load. So the maximum current a motor can take is when it's not turning. Inrush begins here and is not dependant on load, unless ofcourse that load stops the motor turning. Once turning the current drops until some sort of equalibrium is reached. I can't describe that more clearly than in the previous post. -
A Call for Revolution: Supercapacitors in Airsoft
Sewdhull replied to Pseudotectonic's topic in General Discussion
Inrush in this context if the current the motor would take when it's not rotating. When you first apply power the current the motor will take is just the voltage applied divided by the resistance of it's windings. As the motor rotates the magnets create an opposing voltage in the windings which effectively reduces the voltage applied to the windings. As the motor rotates faster there's more opposing voltage until the point where the motor cannot go faster. This is why more voltage spins the same motor faster. The inrush current starts at it's max then reduces as speed increases, because the effective voltage in the windings reduces (the resistance remains the same) until the point is reached where the amount of current becomes stable. Current then rises with load because the voltage reduces as the motor slows because of the load and speed becomes stable at the new load. The power dissipated in the windings increases with the square of the current and this power heats the motor (with some help from the commutator and bearings from friction and contact resistance. Torque, the turning force in the motor, is created the magnetic field generated by the current, interacting with the permanent magnets magnetic field. More current, more torque...Stronger magnets , more torque...more turns, more torque. Higher speed motors go faster than slower ones because they have fewer windings for the permanent magnets to generate an opposing voltage in and so for the same motor speed fewer windings generate less opposing voltage and a faster max speed. You can fit fatter wire on the armature with fewer windings so that the motor can take more current to try to get more torque on a fast motor. More windings is more efficient because the heat (waste) generated is linear with resistance, but exponential with current. I have deliberately avoided things like commutator timing. -
A Call for Revolution: Supercapacitors in Airsoft
Sewdhull replied to Pseudotectonic's topic in General Discussion
No, it was the inrush current that was getting higher that puzzled me. You can equate the inrush current to the current to the current the motor takes when stalled. If there's a big spring stalling the motor the current should be the same if its a small spring. It's possible that different rotor positions on start up mean it takes longer to get going so the current gets closer to the stall current in the time the measurement can be taken, but I don't know. hence the puzzlement. I have a couple of watt meters which will display the current but its not continuous sampling, its periodic. One has a neat graph thing but displays the peak amps also. Setting aside the build quality of motors, high TPA motors with lower currents will always be the most electrically efficient, but if you want speed at the sector gear you'll need appropriate gears, which may not exist for some applications, like a high speed build with a high torque motor. Whilst The NiMH and caps might be outdone by lithium, it is possible that caps and lithium will yield some benefit. Altho part of the rationale was not use lithium for a number of reasons and close the gap between the two types. -
A Call for Revolution: Supercapacitors in Airsoft
Sewdhull replied to Pseudotectonic's topic in General Discussion
Hi, Love that you're doing this type of thing... I concur that C rating is not greatly useful, but IR can be, certainly for comparison. Standard IR measurements are either using DC in 2 stages or an AC meter. I use mine just to monitor battery health. Firstly the variance I mention is from IR calculations, in the IR meter report, using the same current but over different time periods leading to different IR values and another IR value in the C rating report. IR values probably vary more than that depending on who knows what else. We have from about 12 to about 21mOhms. That variance is expected, but it limits the usefulness of IR since it is specific to a set of circumstances. Your table, for the C ratings says they are measurements, the last 3 columns, say nominal values. Nominal current, volts drop and %. You don't discuss your method so it seems like you have measured the IR ,measurements in the table, put it in the table and calculated the nominal values, I realise you have to calculate a %. Nominal is a word used to describe something in name only or a specification, not a measurement or used or actual value. You don't mention the voltage of the batteries but the volts drop of the GPX would indicate 7.4v was used which is not a fully charged battery, unless it was but you used the nominal 7.4v for 2S Lipos. Then when discussing the GPX battery you say it 'would' drop its voltage by half at because of it's IR when 'does' indicate a thing that has happened. You use 'would' again for another battery. Having said the above if you did indeed draw 72A from that pack and halve its voltage and calculated the IR from that, I apologise for the comments. This bit ' not possible to drop voltage and maintain the current' is wrong, I meant something else which is irrelevant if the IR is calculated. I think the C rating can't be used either, it has been my experience that only occasionally has it reflected the current supply ability of the cells. The key when conducting some sort of experiment is for the reader to be able to replicate your experiment so all the necessary information must be present for that to happen. A precise duplication of your results probably wont be possible but the same basis of your experiment must be possible. Standard terminology, a repeatable framework ( aim, hypothesis, method , results, discussion, conclusion). Where you have diagrams or pictures etc, they have to be clear. When looking at the motor current experiment you did, which I really liked over all, there's no baseline motor speed measurement shown but you refer to it and it's relevant as this will tell you where the motors sit in the speed or torque camp. You may not have had the means to measure it, but without it it's harder to make meaningful comparisons. One thing that puzzled me was why the inrush current changed with a stiffer spring, it's not as if the motor windings reduce in resistance to draw more current. Did you do multiple runs or just one of each set up, because you have anomalous results. But great work anyway and valuable. You've probably looked at the Airsoft Trajectory project, a large experiment, a good example. A lot of work tho. Here's an example of a small experiment, https://www.powerstream.com/lithium-phosphate-charge-voltage.htm My background is many years in a lab, a lifetime of engineering, some law enforcement, education and about to take my first pension